There are moving trucks and there are moving trucks. Steve Jordan visited UVB in Warrington to see the latest Matthew James vehicle in work. It’s not an ordinary truck; then again, Matt De-Machen, the company’s owner, is not an ordinary mover.
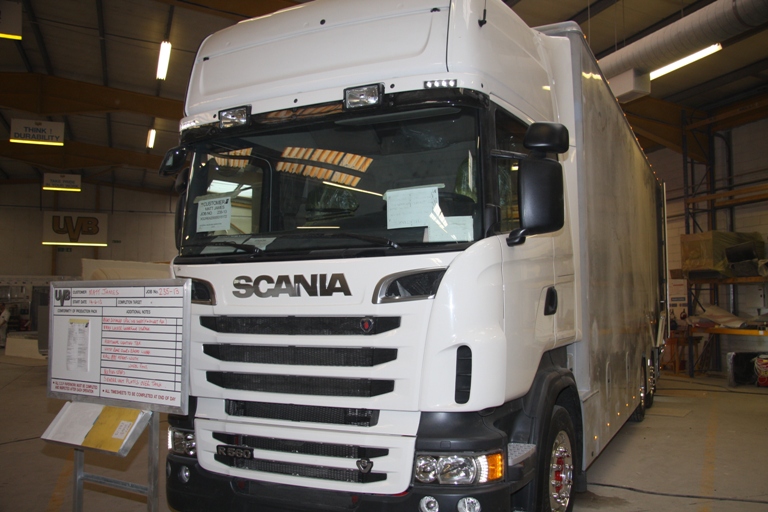
The vehicle epitomises Matt’s love of trucks in general and Scanias in particular. It’s a Scania V8 560, Euro 5, greatly overpowered for the job of hauling the road train to Spain and back but it’s what Matt wanted. Asked why he said: “It’s the best truck there is. It will last me for 12 years and do 1.5 million kilometres.” The engine in particular get’s Matt’s juices flowing. “Everyone goes mad for the Scania V8,” he said. “It’s the sound of them; even with the engine ticking over. The sequence, the way they fire is just amazing. No-one has ever got an engine to sound like a Scania V8.” He’s almost disappointed because the sound proofing on the Scania is so good he can’t hear it properly.
This is the second super road train Matt has built. The first one graces the centre pages of The Mover every month. But he hasn’t always been so fortunate. “I used to run my 210 DAF up and down to Spain with 2,300 cube lorry plus a 600 cube trailer. I used to be sitting in second gear on the hills watching the heater gauge going up. That was lorry driving back in those days. We are spoilt now.”
The new road train has a 26 tonne lorry (five doors) with a 16 tonne trailer (four doors) giving a total carrying capacity of around 3,850 cu ft and a payload of 24 tonnes. There are three axles on the front to avoid any danger of overloading.
The body is constructed of the unique UVB, self produced GRP panelling that gives both structural strength and a smooth outside look. But Matt wanted something more. As the vehicle is mainly used for running to Spain he wanted it to look perfect in any weather conditions. “We made a thicker panel and reduced the pitch of the uprights to give a more solid appearance outside,” explained Terry Sinnott from UVB. “Most GRP bodies are designed to flex with the weather which creates a ripple effect in the summer. But Matt’s truck will look perfectly flat even in Spanish heat.”
Left hand drive makes for easier driving and better safety when in Europe. All the loading doors are on the European kerb side too.
The vehicle is loaded with all the expected extras – and quite a few surprising ones. Air ride suspension all round, for example, gives the best ride and allows the driver to lift the suspension to negotiate high curbs when manoeuvring or for the easy loading of vehicles. Terry said this was very handy when loading flash cars. “If you take the front up and the back down you can easily drive a vehicle in the back using the ramps, even a low car such as a Ferrari.”
The car ramps are stored in a specially designed locker under the vehicle that fits around the chassis geometry and so takes up no space in the load carrying area. They can be retrieved from either side.
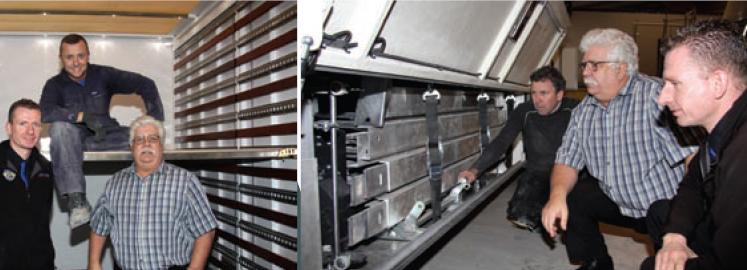
The roof is thicker than normal for additional strength and pillar centres are closer together to give a flatter appearance. UVB also used shallower cross section on the roof and the under frame on the chassis is as low as it can possibly go to give the best possible internal cube. The floor is made from one inch timber with reinforced cross members to handle additional loading weight and provide durability.
The body framework is stainless steel, highly polished and fitted out with LoadLock and decking throughout so the crew can build a floor anywhere to load over cars or fragile loads or to create a separating bulkhead when doing multiple deliveries. “We have done most of these things before, but not for many years,” said Terry. “Some younger members of the industry might not know that these things are possible.”
Now for the extraordinary
So far the specification is impressive, but now it begins to get a bit different.
A 24v winch can be placed in any one of four points (two in the lorry and two in the trailer) for easy loading of cars without risking the smell of a burning clutch. There are LED lights fitted throughout the length of the interior to make loading easy when the light is bad. A separate set of batteries with split charger system powers the lights in the trailer when the lorry is absent so work can continue in a safe working environment. There’s even a time delay switch on the lights so that they cannot be left on overnight and flatten the battery. “We’ve all had the experience of finding a vehicle with a flat battery in the morning,” said Matt. “It can take hours to get it started again and completely disrupt the next day’s work.”
Outside the Project Manager Mark Edwards has stretched the design in directions previously unheard of. There is a special locker for the driver’s diesel gloves so they don’t have to be kept inside the cab; a purpose-built locker for the auxiliary battery in the trailer; alloy wheels all round to reduce weight, improve fuel consumption and look beautiful; high-intensity rear-facing LED lights on both lorry and trailer; very swish little flush covers for the fuel filler that look smart and provide security; and even an external shower to provide a relaxing wash after a hard day’s work in the Spanish sun. “It’s got a 180 litre header tank that should give two weeks of showers,” explained Mark. “It can also be used as a mini jet wash to keep the vehicle clean.”
One key feature Matt has included is an air-operated
sliding beam coupling between the lorry and trailer. This allows the gap between the two bodies to be adjusted to provide extra clearance on tight bends and uneven road surfaces. “If you go around a mountain or across a dip in the road, the road trains can easily hit together at the top causing serious damage.”
But perhaps the star of the accessories show for this vehicle is the permanently fitted external lift. It fits into a specially elongated locker on the lorry, can be assembled in 30 minutes and provides external access to properties up to seven storeys high. “Our Depot Manager Steve Turner had the idea,” said Matt. “He realised that external lifts are used every day in Belgium and Holland. Having our own lift would mean that we wouldn’t have to wait for assistance or incur charges of around £350 a time. Also in Spain it means we can often use the lift to get access to a balcony or terrace and significantly reduce the length of carry.”
But getting it in the locker was a problem. “We did a lot of head scratching,” said Terry. “In the end we switched both fuel tanks to the offside so we could increase the size of the kerb-side locker to accommodate the lift.”
Dressed in red
A feature that few will ever appreciate, except Matt of course, is the chassis paint job. Before it arrived at UVB, the chassis spent five weeks in the paint shop being fully painted in red and lacquered, including the engine, by Lee Atchison at the LA Spray Shop in Barnsley. Nobody can see it from the outside, but Matt knows its there.
Of course the cab comes ready fitted with Scania standard equipment including leather seats, a fridge, freezer and microwave. But for Matt that’s just the starting point. When the vehicle leaves UVB the cab will be subjected to a complete refit the likes of which will probably never have been seen before in the history of the moving industry. The Mover will report on this and the results of the complete body airbrushing, in a future issue.
“This has been the most stress free lorry build I have ever done,” said Matt. “I have built over 60 trucks and this has been the most complex and the easiest. Terry and his team at UVB really know what they are doing and care about getting it right. I really appreciate their professionalism and their attention to detail.”
The truck will be on the road this spring.
Images top to bottom:
-
The Scania under construction at UVB in Warrington;
-
Fuel cover for styling and security;
-
560bhp V8 power: makes a great noise;
-
Right: Shaun Foy demonstrates the LoadLock and decking allowing the crew to build a floor anywhere to load over cars or fragile loads or to create a separating bulkhead when doing multiple deliveries. Left: The external lift fits into a specially elongated locker on the lorry, can be assembled in 30 minutes and provides external access to properties up to seven storeys high;
-
Katie Scott (the painter’s daughter) polishing the red lacquered chassis;
-
The car ramps are stored in a specially designed locker under the vehicle that fits around the chassis geometry and so takes up no space in the load carrying area;
-
An air-operated sliding beam coupling between the lorry and trailer. This allows the gap between the two bodies to be adjusted to provide extra clearance on tight bends and uneven road surfaces;
-
An external shower;
-
Jeff Plume shows the winch positioning for easy car loading.
What makes Unique Van Bodies Unique?
Apparently UVB is the only vehicle body builder in the world that is able to make a single GRP panel, on the premises, up to 46ft x 12ft. This means that continuous body panels are seamless so provide added strength and look great from the outside. There are no external fixings to spoil the appearance or create unsightly dirt trails.
Image: Terry Sinnott with the UVB glass bed where body panels are produced.
If you would like your company profile in The Mover Magazine, please contact nikki@themover.co.uk for more details.
Click here to see the next Editor's pick